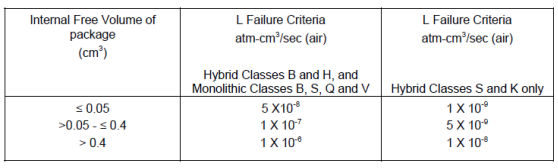
TM 1014 Update and Hermeticity Spec Change
September 28, 2016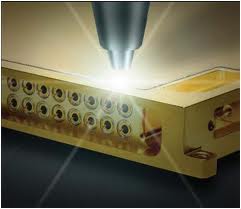
Hermeticity: Frequently Asked Questions
September 29, 2016A Practical Guide to TM 1014 (Seal)
Webinar: Hermeticity Testing For Military and Medical Microcircuits In-Plant TrainingHistory and Background
Microelectronic components used in military, space and Class III medical implants, such as pacemakers, have historically demanded the highest possible levels of quality and reliability. Since the late 1960’s cavity style microelectronic packages intended for use in these systems required a “hermetic” seal. The “hermetic” seal made from glass, ceramic and or metal was designed to keep moisture out of the package, and thereby avoid any failures caused by condensing water vapor inside the cavity. Most military and space systems are designed to last 10-20 years and therefore a “leaky” package represents an unacceptable reliability risk.
Early semiconductor devices and thin film resistor networks in particular were very prone to moisture related failures. In the 1970s several major military programs experienced system level failures due to moisture related problems at the component level. Even today we have reports of Class III implants failing in vivo due to high moisture and loss of hermeticity.
Thirty years ago, Rome Air Development Center (RADC) spearheaded efforts by the USAF to develop test techniques to measure air leak rates and the corresponding build up of moisture in the package1. The theory is to keep the moisture content within the package sufficiently low enough to avoid condensation of water droplets onto the active semiconductor devices. The intended temp range for most military systems is -55 to 125 C. So even a relatively dry package, say 8000 PPM (parts per million) water vapor will form dew inside the package at 5 C (see chart below). These moisture droplets on the surface of the device along with ionic contamination can lead to component failure with catastrophic results at the system level.
As a result, in the late 1960’s the first iteration of Mil-STD-883 Test Method 1014 (Seal) was released 2. The proposed hermeticity test was required, and still is today, on a 100% basis for every part planned for use in a Military or Space system. Over the years the TM 1014 has been revised somewhat, but the basic content remained the same until 1995 when a new technique, Optical Leak Detection (OLT) was introduced. TM 1014.17 (dated 3 May 2018) is the latest revision of the Seal Test Method and forms part of Mil-Std-883L, which is a large document containing many test methods and procedures related to microelectronic components.
TM 1014 assured parts were properly sealed, and if sealed in a dry atmosphere could then pass the corresponding TM 1018 Internal Water Vapor Content or RGA (Residual Gas Analysis). TM 1018 limits the internal moisture content to 5,000 PPM as shown on the chart above. The rationale being that at 5,000 PPM the water vapor dew point is below the freezing mark, and therefore any moisture that would condense out inside the package would be in the form of ice crystals and not be available for corrosion processes. Designers would then have a high confidence that the devices would work as expected for the entire mission life. The purpose of TM 1014 was to verify a hermetic seal and prevent moisture from entering the package.
Today, microelectronic components built on Qualified Manufacturing Lines (QML) intended for Military/Space are governed by Mil-PRF- 38535 Monolithic Microcircuits or Mil-PRF-38534 Hybrids or Mil-PRF-19500 for…